Custom Sculpted Artisan Keycaps: 7 Expert Commission Tips
Master the art of commissioning custom sculpted artisan keycaps.
Custom sculpted artisan keycaps transform your mechanical keyboard into a canvas of personalized art, blending intricate hand‑sculpting with premium materials. Whether you’re commissioning a one‑of‑a‑kind clay figure or a multi‑layered resin sculpture, understanding the process—from concept to installation—is essential. This guide covers everything you need to know about custom sculpted artisan keycaps, including materials, design tips, and care techniques to ensure your bespoke keys look spectacular and last for years.
What Are Custom Sculpted Artisan Keycaps?
Custom sculpted artisan keycaps are individually crafted pieces, often made to order, that replace standard keycaps with miniature sculptures—animals, characters, scenes—on your keyboard. These caps elevate aesthetics and provide tactile uniqueness, making each keystroke a personal statement.
Custom sculpted artisan keycaps go beyond mass‑produced sets by offering hand‑sculpted details in materials like polymer clay and resin. Artisans frequently use two‑part epoxy or high‑grade polymer clays (e.g., Sculpey III) to model figures, then cure or bake them to achieve lasting hardness. Once sculpted, the pieces are often cast in silicone molds for resin reproduction or baked and sealed directly if using clay.
Materials for Custom Sculpted Artisan
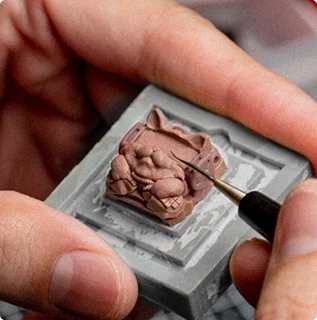
Selecting the right material impacts durability, detail, and finish.
Polymer Clay
Polymer clays—such as Sculpey® or Fimo®—allow fine hand‑sculpted texture and are baked in home ovens. They’re ideal for complex shapes and can be coated with varnish to improve resistance to oils and wear. However, clay caps may chip if subjected to heavy use, so they’re best suited for accent keys.
Resin
Many artisans prefer high‑clarity epoxy resin for multi‑layer pours, embedding miniature sculptures or pigments within clear layers. NASA‑grade resins resist yellowing and offer glass‑like finishes, ensuring that embedded details remain vibrant over time. Resin keycaps require precise mixing ratios and vacuum degassing to avoid air bubbles.
Sculpting Waxes & Hybrid Materials
Advanced makers sometimes use carving waxes (e.g., CX5 hard) to prototype sculptures before molding. Hybrid approaches combining clay armatures with resin casts can yield highly detailed, durable keycaps.
The Commission Process at MCraftin
Commissioning a custom sculpted artisan involves several key steps:
Concept & Reference Gathering
Provide the artisan with sketches, images, or thematic guidelines for your desired sculpture.Quote & Timeline
Artisans factor in sculpting complexity, materials, and batch size to determine pricing (about $20–$50 per cap) and lead times (4–8 weeks).Approval & Prototyping
You’ll receive 3D renders or photos of the clay prototype for feedback before final casting or baking.Production & Quality Control
After approval, the artisan produces resin casts or bakes the final clay piece, then sands, polishes, and finishes each cap. Quality checks ensure stem fit and surface integrity
Design Considerations
Ergonomics & Profile
Custom sculptures must respect keycap profiles (OEM, Cherry, SA, DSA) to maintain ergonomic typing. Most commissions focus on ESC, Enter, or novelty keys to avoid typing interference.
Color & Finish
Pigment choices, translucency, and glazing techniques affect final appearance. Matte sealants produce a soft feel, while glossy coatings enhance depth for resin pours.
Thematic Cohesion
Ensure your custom cap complements your base keyset’s color palette and theme. Coordinate accent colors or sculpted elements to match your overall keyboard aesthetic.
Finishing Techniques
After sculpting or casting:
Sanding & Polishing: Progressive grits remove mold lines and scratches for a smooth finish .
Clear Coating: Apply UV‑resistant spray or epoxy top‑coat to seal and protect against oils and UV damage.
Hand‑Painting: Fine‑tip brushes and acrylic paints allow for detailed highlights (eyes, textures) on resin or baked clay surfaces
Care & Maintenance
To keep custom sculpted artisan keycaps pristine:
Regular Cleaning: Wipe gently with a damp microfiber cloth to remove oils Hirosart.
Avoid Direct Sunlight: Prolonged UV exposure can yellow resin and fade pigments Mihi Mini Studio.
Rotate Usage: Use fragile clay caps on less‑frequented keys (Esc, F‑row) to minimize wear.
Conclusion
Custom sculpted artisan keycaps offer limitless possibilities for personalization, blending artistry and engineering to create functional miniatures on your keyboard. By understanding custom sculpted artisan materials, design principles, and care techniques, you can commission caps that reflect your style and stand the test of time.
Ready to commission your masterpiece? Explore MCraftin’s custom sculpted artisan services and transform your keyboard into a work of art today!